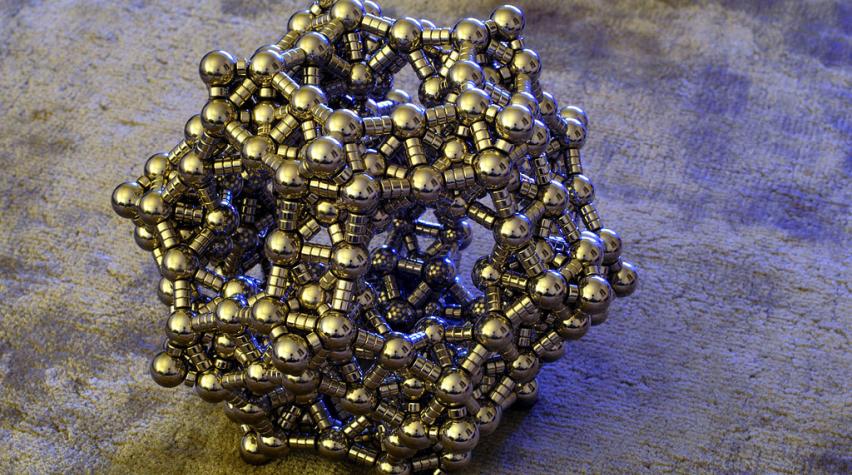
Rare earth metals - the name is actually a bit misleading. It's not so much that the rare earth metals (also known as the lanthanides) are rare; there is actually a relative abundance of them. The real issue is that it's difficult to find economically viable methods by which to process them. While valuable metals such as gold, silver, and platinum are not in the lanthanide family, the rare earth metals are actually extremely valuable in their own right, due to their usefulness in high-tech applications. In fact, a whole session at the 2012 AIChE Annual Meeting last fall was dedicated to the supply chain and sustainability of these critical materials.
Growing demand, waning supply
Peter Dent of Electron Energy Corporation gave an overview of the market supply and demand for rare earth metals. Demand for magnets made from these metals has grown about 7% per year and many of the lanthanides are involved in the production of "green energy" products like hybrid batteries and wind power turbines. Dysprosium, terbium, and neodymium are all classified as critical rare earth materials while samarium, gadolinium and praseodymium are other important rare earth materials. (You can view a presentation about the supply, demand, and uses of rare earth elements here.) Currently China is the largest exporter of rare earth metals, and a drop in Chinese export quotas in July of 2012 brought to the forefront a concern about these critical materials. As prices spiked, people began looking for alternative sources of these important materials. There are actually several locations where these can be mined, including some in the United States. (An earlier post discusses possible new sources for rare earth elements in the US.) The mining of rare earth metal is often ancillary with iron-ore mining, with several sites of this variety in the United States and Malaysia. An additional source of these metals is recycling - or "urban mining." (More about urban mining in this post.) Some areas have recycling programs that make it easy for people to recycle their used electronics but it is still costly to extract the critical metals from those devices. Many areas have recycling programs that charge customers to recycle electronics, so the devices often end up in dumpsters, and thus landfills. (You can see a presentation from the European Union on rare earth elements recycling here.)
Rethinking approach to rare earth elements
With the cost of raw materials increasing, the uncertainty of future supply, and often ineffective recycling programs, companies are beginning to rethink their approach to products that call for these of materials. In the session at the 2012 AIChE Annual Meeting, Anthony Ku of GE Global Research spoke about some of the issues that his company has been exploring. With raw materials accounting for at least half of GE's cost of goods sold, it's no wonder they are getting creative in their approaches to problem solving. The company uses a criticality matrix to evaluate the risks of the materials, including their substitutability, revenue impact, and supply and price risks. One element in particular that was among their highest risk elements was rhenium. Rhenium is used as a dopant in superalloys for aircraft engines. In 2006 there was a huge crunch for this element and prices skyrocketed sixfold, with availability uncertain. GE worked with their suppliers on methods to better recover the element from waste products. They also worked to reduce the quantity of rhenium present in production waste streams and developed processes to recover more of the element from the waste streams. (You can see a presentation by one division of GE concerning rare earth elements here.)