Mentors: nature vs nurture
Huber, who is now one of the world's leading experts on catalytic pyrolysis, summed up the breakthrough's impact": Today, we think that we can be economically competitive with crude oil production." Then he adds the societal dimension: "The ultimate significance of our research is that our green process can be used to make virtually all the petrochemical materials you can find." He finally reveals the another key part of the innovator's toolkit: finding a larger meaning.
Where did Huber find his vision? His relationship with an early mentor offers a clue. In 2005, he earned his PhD at UW-Madison under professor of chemical engineering James Dumesic. While working with Dumesic, Huber specialized in making fuel and chemicals from biomass rather than crude oil. (Start up Virent Energy Systems was spun out of this research)."When I was working on my PhD with Jim Dumesic, he said his goal in coming to the lab each day was that, if we had a good result, it would make a difference. That's the mentality there, of what research should be all about."
After joining the University of Massachusetts-Amherst staff in 2006, Huber helped to develop a single-step process to make olefins and aromatics from biomass using a catalytic fast pyrolysis system. Although he still considers research his main focus; he recentlyamher told
Biorefining Magazine that researchers like him are more than aware of what their work could mean. "I think it is an exciting time to be in this industry," he says. "I think there is a lot of room for growth and improving these processes."
Gallium-Zeolite fast pyrolysis
The newest catalyst may have completely upended the economics of biomass production."The whole name of the game is yield," says Huber. "What amount of aromatics and olefins can I make from a given amount of biomass? Our paper demonstrates that with this new gallium-zeolite catalyst we can increase the yield of those products by 40 percent. This gets us much closer to the goal of catalytic fast pyrolysis being economically viable. And we can do it all in a renewable way."
We think this will be the process of the future everybody will be using for biomass conversion." Huber adds, "This is a $400 billion per year market we're going after. We're making products that already fit into the existing infrastructure that don't need further refining."
In Huber's patented single-step catalytic fast pyrolysis process, biomass is fed into
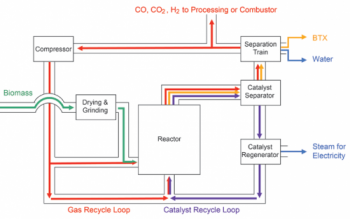
a fluidized-bed reactor, where it thermally decomposes to form vapors. These vapors then enter the team's new gallium-zeolite (Ga-ZSM-5) catalyst, also inside the same reactor, which converts the vapors into the desired chemicals. The economic advantages of the new process are threefold. All of the chemistry occurs in a single reactor; the process uses an inexpensive catalyst; and aromatics and olefins are produced that fit easily into existing petrochemical infrastructures.
Finding a higher calling
To scale up the process to industrial size for the petrochemical industry, the catalytic fast pyrolysis technology has been licensed to New York City's Anellotech, Inc., co-founded by Huber. Again, he reveals his vision for the future to his
alma mater:
"The economics only make sense at large scale, so we need to be processing 2,000 to 3,000 metric tons of dried biomass per day in the biorefinery," Huber says. "You would build the biorefinery in rural locations close to the source. I live in New England. In Maine, we have a lot of paper mills that have been shut down. So we can go to locations like that, that are economically depressed, and build these biorefineries to give a boost to these rural economies."
Improving rural economies, building a more sustainable environment; few researchers try to make such an impact through their work. For Huber, it is the role of the engineer to provide solutions.
Using this new catalyst, how close is the catalytic fast pyrolysis technology to going commercial? "Close," says Huber.
Photo: Huber at desk - Umass, John Solem/ Bioengineeringmagazine Graphic: Process schematic, Anellotech Photo: Huber holds flask: Umass Photo: Huber in lab - Umass